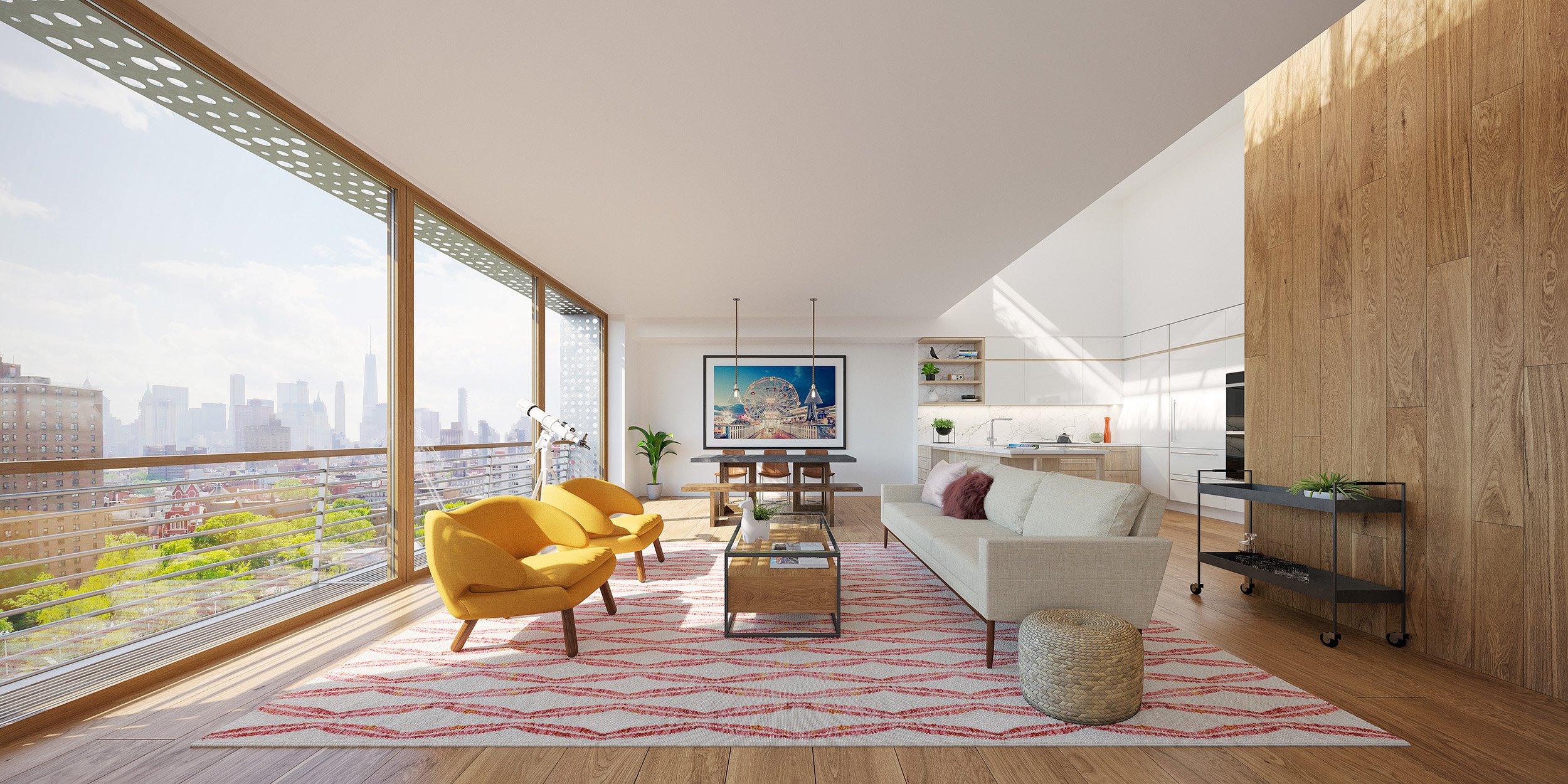
Mass Timber Multi-Family
New York, NY
By combining the benefits of CLT construction and Passive House design, we reduced both the anticipated embodied energy and the operational energy of the building by over 70%
The Challenge
By introducing innovative and sustainable building techniques in a design that balances the existing character and scale of the neighborhood, ZH hopes these principles influence the nature of future development in the neighborhood.
The project is located within a DEC Potential Environmental Justice Area, and although it is not within a Disadvantaged Community, it is neighbored on three sides by blocks that are. New York City is also a Clean Energy Community and the project meets the New York State Energy Stretch Code 2020. The Lower East Side neighborhood where the project is located is rapidly changing with a mix of luxury and supportive housing. By introducing innovative and sustainable building techniques in a design that balances the existing character and scale of the neighborhood, ZH hopes these principles influence the nature of future development in the neighborhood.
Standing at eight floors tall, the project houses full floor residential units with views of downtown Manhattan. Facade design features such as the steel railings and the horizontal shading devices at the windows are a careful deliberation between meticulous shading analyses and aesthetics. This innovative project was first designed as a mass timber Passive House and was awarded a USDA Wood Innovations Grant to further research and develop this highly sustainable construction strategy. By combining the benefits of CLT construction and Passive House design, ZH Architects reduced both the anticipated embodied energy and the operational energy of the building by over 70%. In practice this reduces its carbon footprint and minimizes the energy and expense required to maintain comfortable living spaces within. This level of energy efficiency brings this building in line with Mayor DeBlasio’s bold plan to reduce the city’s green house gas emissions by 80% by 2050.
The project was designed to meet PHI’s Plus standards, which means that the building meets Passive House standards for energy conservation and provides on-site renewable energy through photo-voltaic panels which are installed on the roof. In addition to these operational energy savings, the project was designed to be a mass timber structure which also provides benefits in embodied energy and carbon sequestering. As designed the project had the potential to reduce life cycle carbon emissions by a total of 3,817 tons, the equivalent of removing 806 cars from the road.
Recognition
USDA Forestry Grant
Unlike concrete and other conventional construction materials, CLT panels can be prefabricated at an offsite manufacturing facility and then installed in a shorter time frame which saves time and money
Resiliency and Passive and Active Survivability:
In response to the south facing orientation on a wide street, horizontal shading devices were implemented to provide shading during the warm summer months while allowing solar heat-gains in the winter months. This passive solar strategy is coupled with highly insulated and air-tight wall construction which maintains comfortable indoor air temperatures in a power outage situation. In addition, the photovoltaic panels provide on-site renewable energy, which can be used to power life-critical devices and equipment if the power grid is down.
Non-Energy Co-Benefits:
The project is located along the bustling traffic of Houston Street and is in an E-Designated area for noise and air pollution area as determined by the New York City Office of Environmental Remediation. The Passive House standards are perfectly suited to provide co-benefits in instances like this, where the insulated and air sealed construction methods enable energy efficient heating and cooling while also providing improved indoor air quality and noise reduction. The Passive House building also reduces the threat of pests entering the building, and the solar array on the roof is elevated so that the roof can be occupied while the solar panels provide shade for occupants enjoying a shared outdoor space.
Embodied Carbon and Global Warming Potential:
ZH Provided embodied energy analysis using the Athena program to track the lower carbon emissions of mass timber versus concrete. The study revealed that the project reduced the carbon emissions by 3,817 tons or the equivalent of taking 806 cars off the road.
Replicability, Scalability, and Market Transformation:
One of the barriers to building in the city is the high cost of construction, with of course the added impact of emissions and noise pollution. One the ways we can reduce this congestion and expense is to prefabricate in a factory and erect on site with a reduced footprint. This project and associated grant explored this by designing a factory-built CLT structure and erecting with a reduced timeline and smaller crew. The CLT is being made in rural communities and hence redistributes labor to underemployed communities.
The USDA grant allowed the team to study the cost and construction timeline difference between a concrete and CLT structure. During our design development meetings, we were told that a mass timber structure would be more costly to build but would saved time to erect. What we found was that the cost was actually less for the mass timber strategy, not including the time saved. Mass timber offers reduced soft costs as well as other environmental benefits like less construction dust and noise. As a result of recent NYC code change and the knowledge gained from this project, our office is, where possible, actively converting projects to mass timber construction.
Features
-
Modular Construction
-
High-Performance Envelope
-
HRV (Energy Recovery Ventilator)
-
Solar Panels
-
Triple-Glazed Windows
-
Thermal Bridge Reduction